“Cable assemblies!”
What usually enters someone’s head when they hear that phrase? Ethernet patch cable assemblies? Standard video cables assemblies like HDMI, DVI, miniDP or even VGA that link a laptop or tablet to an LCD Projector or wall-mount TV? Probably.
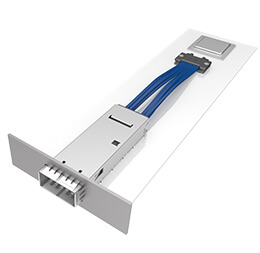
In the world of high-speed cable assemblies, Samtec has found a unique nitch for itself. While most Samtec competitors focus on industry-standard or high-volume application-specific cable assemblies, Samtec focuses on customized high-speed cable assemblies.
Samtec combines its vertically integrated cable manufacturing plant with our Advanced Interconnect Design capabilities built to customer specifications.
Samtec’s in-house cable and custom cable assembly capabilities include:
- Micro-coax and twinax design, development and volume manufacturing
- Advanced R+D and signal integrity expertise
- Interconnect design, development and volume manufacturing
- Vertically integrated, quick-turn product and volume manufacturing
This vertical integration allows for the ultimate combination of design flexibility and customer service.
Advantages of Samtec’s model include:
- Shorter, controlled lead times
- Highest quality product
- Optimized performance
- In-house impedance controlled PCB design and processing
- Unparalleled pricing and delivery
Samtec’s Wilsonville, OR cable facility focuses on R&D and manufacturing of precision extruded micro coax and twinax cable used for high-speed, high-density cable assemblies, including 26-38 AWG, 50/75/85/100 Ω impedance, and systems rated at 28 Gbps and beyond.

One focus area of Samtec’s R+D is solid center conductor co-extruded twinax cables. Solid center conductor cores offer better dielectric properties when compared to stranded center conductors. This leads to enhanced performance such as ultra-low skew and higher data rates.
Other advantages include:
- Provides optimal diameter control capability for tighter tolerances and consistency
- Eliminates stranding variations, providing more consistent dielectric uniformity to conductor for ULS performance
- Significantly lower cost (up to 60% lower)
- Improves preparation and termination quality during assembly
- Allows new termination techniques during assembly for superior interconnect
- Resistance
- Laser bonding