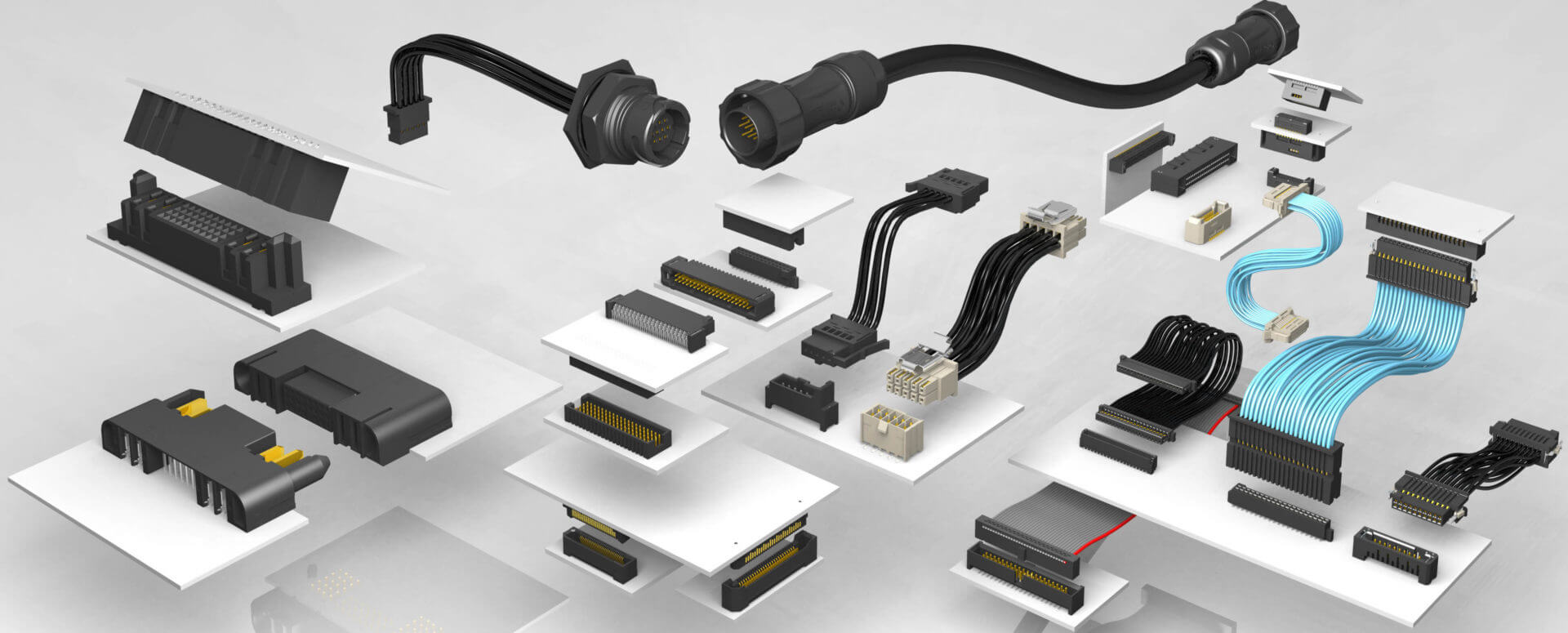
Our friends at Connector Supplier keep the world up-to-date on everything in the connector universe. They recently ran an article from Samtec entitled Rugged Industrial Interconnects: The Design Behind The Description.
Many industrial electronics OEM designers use the word “rugged” to describe their board-level interconnect needs. While rugged can mean different things to different people, it usually includes the ability to withstand high shock and vibration applications, maintain mechanical and electrical integrity after exposure to both harsh environments and high mating cycles, and provide EMI shielding attributes, to name a few.
This article explains that connectors that exhibit the rugged, high-reliability performance characteristics required to withstand hazards including shock, vibration, and high mating cycles in harsh industrial applications don’t happen by chance. Design features including contacts, plating materials, and insulators are critical to achieving and selecting rugged industrial interconnects.
Topics covered include:
- Contact designs and comparisons
- Common base metals for contacts — brass, phosphor bronze, and beryllium copper — and the pros and cons of each
- Contact design for bandwidth — contact geometry, mating surfaces, and positioning in the insulator
- Which plating to choose, and how the best plating finish for your application is whichever material meets your requirements at the lowest cost
- There’s a quick discussion of when to use gold, tin, and selective platings
- And finally we discuss plastic insulator design features that are popular with industrial product designers, including board locks, positive latching systems, screw downs, weld tabs, and IP ratings, to name a few.
And speaking of rugged designs, let me take this opportunity to introduce Samtec’s newest latching and locking options. We feel these are the most secure latching and locking systems in the industry. Just don’t lose the key …
Other links that may be of interest: